Aluminum-core printed circuit boards and copper-core PCBs are common in various electronic devices. An aluminum core PCB consists of a thin layer of aluminum bonded to a non-conductive substrate material, typically a layer of fiberglass-reinforced epoxy resin. In contrast, a copper core PCB features a layer of copper sandwiched between two layers of the non-conductive substrate material.
One of the main advantages of aluminum core PCBs is their excellent thermal conductivity, which makes them ideal for applications that require efficient heat dissipation, such as LED lighting and power electronics. Additionally, aluminum-core PCBs have a lower manufacturing cost than copper-core PCBs.
On the other hand, copper core PCBs offer superior mechanical strength and durability, making them ideal for high-power applications that require high current-carrying capacity and resistance to physical stress. They are commonly used in power supplies, automotive electronics, and high-performance computing applications.
Overall, the choice between aluminum core PCBs and copper core PCBs depends on the application’s specific requirements, including factors such as thermal management, mechanical strength, and cost.
The Benefits and Advantages of Aluminum Core PCBs
First – let’s talk aluminum PCBs! As the name suggests, these boards use an aluminum core instead of the traditional copper core. An aluminum backing provides the base for the PCB laminate and copper traces to be built up on top.
Now you’re probably wondering – what are the benefits of using aluminum rather than copper as the core material? There are three main advantages aluminum PCBs offer:
First and foremost, aluminum has excellent thermal conductivity, even better than copper! This makes aluminum PCBs ideal for heat dissipation in high-power applications like LEDs and power electronics. The aluminum core acts like a built-in heatsink to draw heat away from sensitive components.
Second, aluminum is super lightweight, around 3 times lighter than copper. So, aluminum PCBs are a fantastic solution to reduce weight for products where weight matters, like aerospace, aviation, and automotive.
Lastly, aluminum raw material and fabrication costs are lower than copper. So, aluminum can be a more budget-friendly material option for cost-sensitive applications.
In summary, aluminum PCBs are great for outstanding thermal performance, lightweight boards, or lower cost. Make sense why we specialize in aluminum PCBs now? Let’s move on and look at traditional copper core PCBs next!
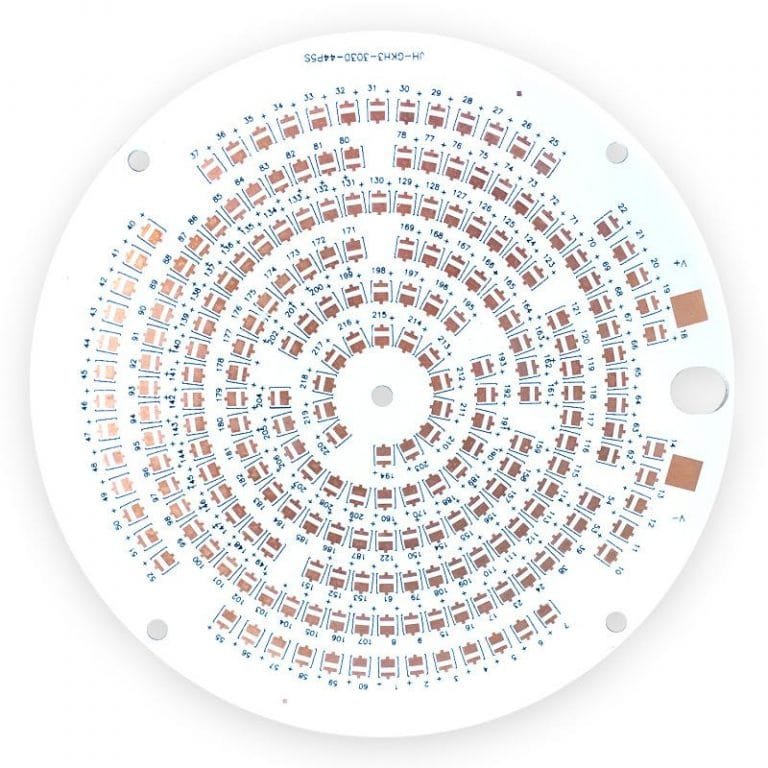
An Overview of Traditional Copper Core PCBs
Now, let’s switch gears and talk about the copper core PCBs that have been the standard for many decades. As the name describes, copper core PCBs use a base copper layer as the foundation for building up the laminate dielectric and etched copper circuitry on top.
Compared to aluminum, copper has two main advantages:
- Copper has superior electrical conductivity, which allows copper PCBs to handle more complex and higher-speed circuit designs. The high conductivity enables efficient transmission of signals across the board.
- Copper PCBs have a long history of use and maturity in the industry. This means there are well-established manufacturing processes and supply chains for copper PCB production globally. Copper core is considered the ‘safe’ and ‘standard’ option for PCBs.
So, in summary, the pros of copper PCBs are excellent electrical performance and widespread availability. These make copper a versatile choice for many applications, especially those with complex digital circuits or signals.
Key Differences Between Copper and Aluminum PCBs
Materials
The material composition of aluminum and copper core PCBs is different, and each type has advantages and limitations.
An aluminum core PCB consists of a thin layer of aluminum that is typically between 0.5mm to 3mm thick, which is bonded to a non-conductive substrate material such as fiberglass-reinforced epoxy resin. The aluminum layer provides excellent thermal conductivity, allowing heat to dissipate rapidly from the PCB. The substrate material provides mechanical support and electrical insulation. The main advantages of aluminum core PCBs include their high thermal conductivity, lightweight construction, and low cost. However, they are unsuitable for applications requiring high mechanical strength or resistance to physical stress.
In contrast, a copper core PCB features a layer of copper, typically 1 oz. to 10 oz. Thick sandwiched between two layers of non-conductive substrate material. Copper core PCBs have higher mechanical strength than aluminum core PCBs, making them suitable for applications requiring high current-carrying capacity and resistance to physical stress. Copper also has good thermal conductivity but is not as high as aluminum. The main advantages of copper core PCBs include their superior mechanical strength, durability, and suitability for high-power applications. However, they are more expensive to manufacture than aluminum-core PCBs.
The choice between aluminum core PCBs and copper core PCBs depends on the application’s specific requirements. Aluminum core PCBs are ideal for applications that require efficient heat dissipation, such as LED lighting and power electronics, while copper core PCBs are suitable for applications that require high mechanical strength and durability, such as power supplies, automotive electronics, and high-performance computing.
Thermal Conductivity Properties
Aluminum and copper core PCBs have different thermal conductivity properties, affecting their performance in applications that generate heat.
Aluminum core PCBs have excellent thermal conductivity due to the high thermal conductivity of aluminum, which is approximately three times higher than copper. The thermal conductivity of aluminum ranges from 160 to 220 W/mK, while copper ranges from 385 to 401 W/mK. This means that aluminum core PCBs can quickly dissipate heat generated by electronic components, making them ideal for applications that require efficient heat management. Additionally, aluminum core PCBs have a lower thermal expansion coefficient than copper, which means they are less prone to warping or cracking due to temperature changes.
Copper core PCBs also have good thermal conductivity, but not as high as aluminum core PCBs. However, copper core PCBs have higher thermal mass, which allows them to absorb more heat energy before reaching their thermal limit. This makes them ideal for heat applications, such as power electronics. Additionally, copper-core PCBs have better mechanical strength than aluminum-core PCBs, which means they can withstand higher temperatures and physical stress without degrading.
Overall, the choice between aluminum core PCBs and copper core PCBs depends on the specific thermal management requirements of the application. Aluminum core PCBs are ideal for applications that require efficient heat dissipation, while copper core PCBs are more suitable for high-power applications that require high current-carrying capacity and resistance to physical stress.
Electrical Conductivity
Copper has about 20% higher electrical conductivity than aluminum. This gives copper the edge for high-frequency signals and complex circuit boards.
Weight
Aluminum is approximately 3 times lighter in weight than copper. So for lightweight designs, aluminum provides a significant weight reduction.
Mechanical Strength Properties
Aluminum and copper core PCBs also differ in their mechanical strength properties, which are important considerations in applications that require durability and resistance to physical stress.
Aluminum core PCBs have a lower mechanical strength compared to copper core PCBs. This is because aluminum is a soft metal, making it more susceptible to deformation and damage from physical stress. Additionally, aluminum has a lower hardness than copper, making it more prone to wear and tear over time. However, aluminum core PCBs are lightweight, which can be advantageous in applications where weight is a concern.
Copper core PCBs have higher mechanical strength than aluminum core PCBs due to the greater hardness of copper. Copper core PCBs are more resistant to deformation and damage from physical stress, which makes them suitable for high-current applications that require durability. Additionally, copper has better wear resistance than aluminum, meaning copper core PCBs are less likely to experience wear and tear over time.
In summary, the choice between aluminum core PCBs and copper core PCBs for mechanical strength depends on the application’s specific requirements. Aluminum core PCBs are suitable for applications that prioritize weight over mechanical strength. In contrast, copper core PCBs are ideal for high-current applications requiring durability and physical stress resistance.
Manufacturing Cost
Aluminum and copper core PCBs also differ in their manufacturing cost, which is an important consideration in selecting the most suitable type of PCB for a given application.
Regarding material cost, aluminum is generally less expensive than copper, making aluminum-core PCBs more cost-effective than copper-core PCBs. Aluminum is widely available and less expensive to mine and refine than copper, a rarer and more expensive metal. Additionally, the thermal conductivity of aluminum allows for the use of thinner copper layers, which reduces the overall cost of the PCB.
However, the cost of manufacturing aluminum core PCBs is higher than that of copper core PCBs. Aluminum is a softer metal than copper, making it more challenging to machine and process. The manufacturing process of aluminum core PCBs involves specialized equipment and techniques that add to the overall cost. Copper core PCBs are easier to manufacture, as copper is a harder metal and is more widely used in the industry.
Overall, the choice between aluminum core PCBs and copper core PCBs for manufacturing cost depends on the application’s specific requirements. If material cost is the primary concern, aluminum core PCBs are more cost-effective. However, if manufacturing cost is the primary concern, copper core PCBs may be a better choice due to their ease of manufacture.
Applications
Aluminum and copper core PCBs have different applications and are suitable for different scenarios due to their unique properties and characteristics.
Aluminum core PCBs are typically used in applications where heat dissipation is critical, such as LED lighting, power supplies, and automotive electronics. Aluminum has high thermal conductivity allows it to dissipate heat more effectively than other materials, making it an ideal choice for heat-intensive applications. Additionally, aluminum core PCBs are lightweight, which can be advantageous in applications where weight is a concern.
On the other hand, copper core PCBs are more suitable for high-current applications that require durability and resistance to physical stress, such as power amplifiers, motor drives, and high-power LED lighting. Copper has a higher electrical conductivity than aluminum, so it can handle higher current loads without overheating. Additionally, copper has better wear resistance than aluminum, making it less likely to experience wear and tear over time.
In terms of cost-effectiveness, aluminum core PCBs are generally more cost-effective than copper core PCBs due to the lower cost of aluminum. However, the cost of manufacturing aluminum core PCBs is typically higher than copper core PCBs due to the challenges involved in machining and processing aluminum.
In summary, the choice between aluminum core PCBs and copper core PCBs depends on the application’s specific requirements. Aluminum core PCBs are suitable for applications that require heat dissipation and prioritize weight, while copper core PCBs are ideal for high-current applications that require durability and resistance to physical stress. Both types of PCBs have their advantages and disadvantages and should be carefully evaluated before making a decision.
Conclusion
The comparison table summarizes the advantages and disadvantages of Aluminum Core PCB and Copper Core PCB in different aspects.
Comparison | Aluminum Core PCB Advantages | Copper Core PCB Advantages |
---|---|---|
Thermal Conductivity | High thermal conductivity, good heat dissipation performance | Higher electrical conductivity, more suitable for high current applications |
Mechanical Strength | Lighter weight, suitable for applications with lower weight requirements | Harder, more wear-resistant, suitable for high-load applications |
Manufacturing Cost | Lower material cost, suitable for mass production | Lower manufacturing cost, suitable for small-scale production |
Application Area | LED lighting, power supply, automotive electronics, and other scenarios that require heat dissipation | Power amplifiers, motor drivers, high-power LED lighting, and other high-current scenarios |
In conclusion, Aluminum Core PCB and Copper Core PCB have different advantages and disadvantages. Aluminum Core PCB is suitable for use in scenarios that require efficient heat dissipation and lower weight, such as LED lighting, power supply, and automotive electronics. On the other hand, Copper Core PCB is more suitable for high current and high mechanical stress scenarios, such as power amplifiers, motor drivers, and high-power LED lighting. The two are relatively close in terms of manufacturing cost, but Aluminum Core PCB may be more cost-effective for mass production.
Therefore, when choosing the appropriate PCB type, it is necessary to consider the specific application scenarios and requirements comprehensively. If efficient heat dissipation or lower weight requirements are needed, it is recommended to choose Aluminum Core PCB. If high current or mechanical stress needs to be handled, it is recommended to choose Copper Core PCB.
Are you looking for a reliable PCB manufacturing partner who can provide high-quality Aluminum Core PCB, Copper Core PCB, Heavy Copper PCB prototypes, and low-to-high volume PCB manufacturing services? Look no further than our company!
We are dedicated to providing our customers with the best PCB solutions, and our state-of-the-art manufacturing facilities and experienced engineers ensure that we deliver high-quality PCBs that meet our customers’ exact specifications.
Whether you need Aluminum Core PCBs for efficient heat dissipation in LED lighting or automotive electronics, Copper Core PCBs for high-current applications, or Heavy Copper PCBs for high-power applications, we have the expertise and resources to meet your needs.
So, if you’re ready to partner with a trusted and reliable PCB manufacturer, contact us today to get started!