What Are IMS PCBs?
In the ever-evolving world of electronics, thermal management remains a critical challenge. This is where Insulated Metal Substrate (IMS) PCBs come into play, offering a revolutionary solution for heat dissipation. As a leading IMS PCB manufacturer, JHYPCB is at the forefront of this technology, providing cutting-edge solutions for various industries.
What exactly is an IMS PCB? An Insulated Metal Substrate PCB, also known as a thermal PCB or metal core PCB, is a specialized circuit board designed to efficiently transfer heat away from components. Unlike traditional FR-4 PCB boards, IMS PCBs are engineered with thermal management as a primary focus.
The key components of an IMS circuit board include:
- Metal Base Layer: Typically made of aluminum or copper, this layer acts as a heat spreader.
- Thermally Conductive Dielectric Layer: A thin, electrically insulating layer that allows heat transfer.
- Circuit Layer: The top copper foil where the circuit pattern is etched.
As an experienced IMS PCB manufacturer, JHYPCB understands that the advantages of IMS PCBs over traditional PCBs are numerous:
- Superior Heat Dissipation: IMS PCBs can dissipate heat up to 8-10 times more effectively than standard FR-4 boards.
- Improved Reliability: Better thermal management leads to longer component life and increased overall system reliability.
- Space Efficiency: The excellent heat dissipation allows for more compact designs, eliminating the need for bulky heat sinks in many applications.
- Cost-Effectiveness: While initial costs may be higher, the long-term benefits often result in overall cost savings.
These advantages make IMS PCBs the go-to choice for applications involving high-power components or those operating in challenging thermal environments. As a trusted IMS PCB manufacturer, JHYPCB has been providing these high-performance boards to industries ranging from automotive and aerospace to LED lighting and renewable energy.
In the following sections, we’ll delve deeper into the materials used in IMS PCB manufacturing, explore various applications, and showcase how JHYPCB, as a premier IMS PCB manufacturer, can meet your specific needs. Whether you’re looking for prototype development or large-scale production, our expertise in IMS PCB manufacturing ensures you’ll receive top-quality boards tailored to your exact specifications.
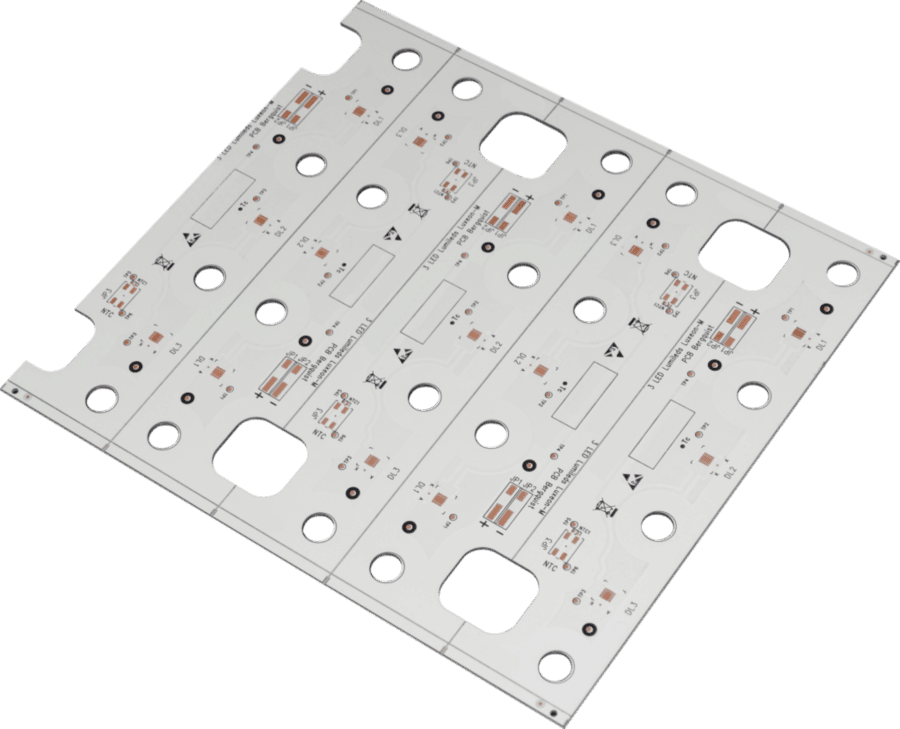
IMS PCB Materials: Exploring the Options
As a leading IMS PCB manufacturer, JHYPCB understands that the choice of materials is crucial in IMS PCB production. The right materials can significantly impact the performance and reliability of your final product. Let’s explore the options available and how they affect your IMS PCB’s thermal management capabilities.
Common IMS PCB Materials:
- Aluminum-based IMS PCBs: Aluminum is the most widely used base material in IMS PCB manufacturing. As an experienced IMS PCB manufacturer, we often recommend aluminum for its excellent balance of thermal conductivity, weight, and cost-effectiveness. Aluminum IMS PCBs are ideal for LED lighting applications and consumer electronics.
- Copper-based IMS PCBs: For applications requiring superior thermal performance, copper-based IMS PCBs are the go-to choice. While more expensive than aluminum, copper offers nearly twice the thermal conductivity. As a versatile IMS PCB manufacturer, JHYPCB can produce copper IMS PCBs for high-power applications in industries like automotive and aerospace.
- Other Metal Core Options: As an innovative IMS PCB manufacturer, we also work with other materials like steel or alloys for specialized applications. These materials can offer unique properties such as increased strength or magnetic shielding.
Comparison of Thermal Conductivity:
When selecting an IMS PCB material, thermal conductivity is a key factor. Here’s a quick comparison:
- Aluminum: 150-180 W/mK
- Copper: 380-400 W/mK
- FR-4 (traditional PCB): 0.3 W/mK
As you can see, both aluminum and copper offer significantly better thermal performance than traditional FR-4 boards. For a more in-depth understanding of thermal conductivity in PCB materials, you can refer to this comprehensive guide from Altium.
Selecting the Right Material for Your Application:
As your trusted IMS PCB manufacturer, JHYPCB can help you choose the ideal material for your specific needs. Consider the following factors:
- Thermal Requirements: How much heat does your application generate?
- Cost Constraints: What’s your budget for materials?
- Weight Considerations: Is the weight of the PCB a critical factor?
- Environmental Factors: Will the PCB be exposed to harsh conditions?
Our team of experts at JHYPCB is always ready to contact us to discuss your project requirements and recommend the best IMS PCB material solution. As an IMS PCB manufacturer with years of experience, we’ve worked on a wide range of projects across various industries, giving us the knowledge to guide you towards the optimal choice.
Remember, the right IMS PCB material can make a significant difference in your product’s performance and lifespan. Trust JHYPCB, your reliable IMS PCB manufacturer, to provide you with high-quality, thermally efficient PCBs tailored to your exact specifications. Whether you need a small batch of prototypes or large-scale production, our state-of-the-art manufacturing facilities are equipped to deliver excellence in every IMS PCB we produce.
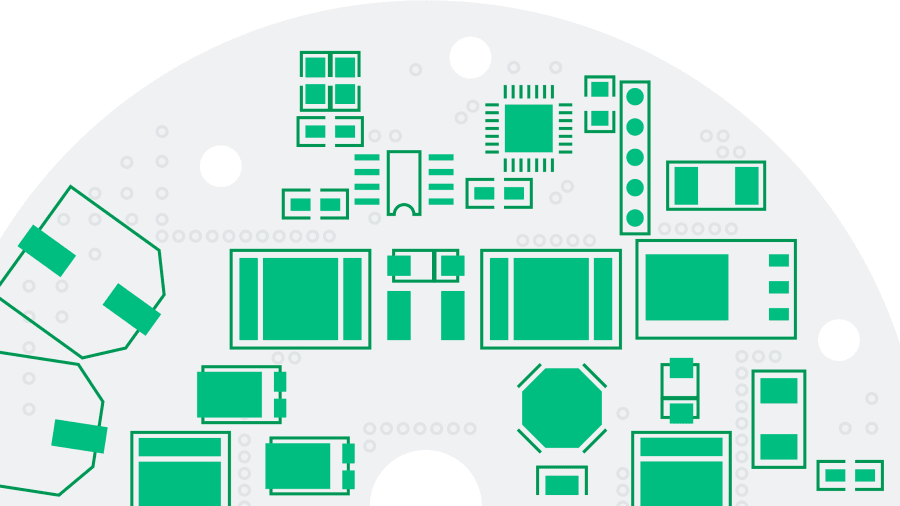
Applications of IMS PCBs
As a leading IMS PCB manufacturer, JHYPCB has witnessed firsthand the growing adoption of IMS technology across various industries. The superior thermal management capabilities of IMS PCBs make them ideal for applications where heat dissipation is critical. Let’s explore some key areas where our expertise as an IMS PCB manufacturer has made a significant impact:
- LED Lighting Industry: The LED lighting sector has been revolutionized by IMS PCB technology. As an experienced IMS PCB manufacturer, we’ve seen a surge in demand for these boards in LED applications. IMS PCBs efficiently dissipate heat generated by high-power LEDs, ensuring longer lifespan and better performance.
- Power Electronics: In the realm of power electronics, thermal management is paramount. As a trusted IMS PCB manufacturer, JHYPCB provides solutions for power supplies, motor drives, and inverters. Our IMS PCBs help these high-power devices operate more efficiently and reliably, reducing the risk of thermal runaway and extending component life.
- Automotive Sector: The automotive industry is another area where our expertise as an IMS PCB manufacturer shines. From electric vehicle (EV) battery management systems to advanced driver-assistance systems (ADAS), IMS PCBs play a crucial role. They help manage the intense heat generated in these applications, ensuring safety and reliability in challenging automotive environments.
- Aerospace and Defense: In aerospace and defense applications, reliability is non-negotiable. As a precision-focused IMS PCB manufacturer, JHYPCB delivers boards that meet the stringent requirements of these industries. Our IMS PCBs are used in radar systems, avionics, and satellite communications, where they help manage heat in compact, high-performance electronic systems.
- Renewable Energy Systems: The renewable energy sector, particularly solar inverters and wind power systems, benefits greatly from IMS PCB technology. As an environmentally conscious IMS PCB manufacturer, we’re proud to contribute to the efficiency and longevity of green energy solutions. Our IMS PCBs help these systems operate more efficiently, even in harsh outdoor conditions.
For a comprehensive overview of PCB applications across various industries, you might find this industry guide from PCB Solutions informative.
At JHYPCB, we don’t just manufacture IMS PCBs; we provide thermal management solutions tailored to your specific application. Our experience as a versatile IMS PCB manufacturer allows us to understand the unique challenges of different industries and offer customized solutions.
Whether you’re developing cutting-edge LED products, working on next-generation automotive electronics, or pushing the boundaries in aerospace technology, JHYPCB is your go-to IMS PCB manufacturer. We combine industry expertise with state-of-the-art manufacturing capabilities to deliver IMS PCBs that meet and exceed your expectations.
Ready to explore how our IMS PCB solutions can enhance your product’s performance? Contact our team of experts today. As your trusted IMS PCB manufacturer, we’re here to guide you through the process, from material selection to final production, ensuring you get the perfect IMS PCB for your application.
JHYPCB: Your Expert IMS PCB Manufacturer
At JHYPCB, we pride ourselves on being more than just an IMS PCB manufacturer – we’re your partner in innovation and quality. Our years of experience as a leading IMS PCB manufacturer have equipped us with the knowledge and skills to deliver superior products tailored to your specific needs.
Manufacturing Capabilities:
As a cutting-edge IMS PCB manufacturer, JHYPCB boasts state-of-the-art facilities that enable us to produce high-quality IMS PCBs with precision and efficiency. Our advanced equipment allows us to handle a wide range of specifications:
- Board thickness: 0.2mm to 5.0mm
- Copper thickness: 1oz to 10oz
- Maximum board size: 610mm x 1200mm
- Minimum trace width/spacing: 3mil/3mil
Our capabilities as an IMS PCB manufacturer extend beyond just production. We offer comprehensive DFM guidelines to ensure your IMS PCB meets all thermal and electrical requirements from the outset.
Quality Control Processes:
Quality is at the heart of everything we do as an IMS PCB manufacturer. Our rigorous quality control processes ensure that every IMS PCB leaving our facility meets the highest standards:
- Raw Material Inspection: We source only the best materials from trusted suppliers.
- In-Process Quality Checks: Our production line features multiple checkpoints to catch any issues early.
- Thermal Performance Testing: We conduct thorough thermal simulations and real-world tests to verify heat dissipation capabilities.
- Electrical Testing: Every board undergoes electrical testing to ensure functionality.
- Final Inspection: Our quality assurance team performs a comprehensive final check before shipment.
For more information on PCB quality standards, you might find this guide from IPC (Association Connecting Electronics Industries) helpful.
Customization Options:
As a flexible IMS PCB manufacturer, we understand that one size doesn’t fit all. That’s why we offer a range of customization options:
- Custom dielectric thickness for specific thermal requirements
- Various surface finishes including ENIG, HASL, and OSP
- Selective plating for enhanced thermal performance in critical areas
- PCB assembly services for a complete turnkey solution
Prototype and Volume Production Services:
Whether you need a small batch of prototypes or large-scale production, JHYPCB has you covered. As a versatile IMS PCB manufacturer, we offer:
- Quick-turn prototyping services for faster time-to-market
- Scalable production capabilities to meet growing demand
- Consistent quality from prototype to volume production
Our commitment as your trusted IMS PCB manufacturer goes beyond just delivering boards. We strive to build long-term partnerships, offering ongoing support and continuously improving our processes to meet your evolving needs.
Ready to experience the JHYPCB difference? As your dedicated IMS PCB manufacturer, we’re here to bring your innovative ideas to life. Get in touch with our team today to discuss your IMS PCB requirements. Let’s work together to create high-performance, thermally efficient PCB solutions that give your products a competitive edge in the market.
Remember, when you choose JHYPCB as your IMS PCB manufacturer, you’re not just getting a product – you’re gaining a partner committed to your success. Let our expertise as a leading IMS PCB manufacturer drive your next project to new heights of performance and reliability.
The IMS PCB Manufacturing Process
As a leading IMS PCB manufacturer, JHYPCB has refined our manufacturing process to ensure the highest quality and reliability in every board we produce. Understanding this process can help you appreciate the complexity and precision that goes into creating these high-performance thermal management solutions. Let’s walk through the key steps we take as an expert IMS PCB manufacturer.
Step-by-Step Explanation of the Production Process:
- Design and Engineering: The process begins with careful design and engineering. As an experienced IMS PCB manufacturer, we work closely with our clients to optimize their designs for thermal performance. This stage often involves thermal simulations to ensure the IMS PCB will meet the required heat dissipation specifications.
- Material Selection: Based on the design requirements, we select the appropriate materials. As a versatile IMS PCB manufacturer, we offer a range of base metals and dielectric materials to suit different thermal and cost requirements.
- Base Metal Preparation: The chosen metal base (typically aluminum or copper) is cleaned and prepared for bonding with the dielectric layer. This step is crucial for ensuring good adhesion and thermal transfer.
- Dielectric Layer Application: A thin layer of thermally conductive yet electrically insulating material is applied to the metal base. The precision of this step is critical, as the dielectric layer’s thickness affects both the thermal performance and the electrical isolation of the final IMS PCB.
- Copper Foil Lamination: High-quality copper foil is laminated onto the dielectric layer. This forms the basis for the circuit pattern.
- Imaging and Etching: The circuit pattern is transferred onto the copper layer using photolithography techniques. Unwanted copper is then etched away, leaving the desired circuit pattern.
- Plating and Finishing: Additional plating may be applied to enhance conductivity or prepare the surface for component assembly. Various surface finishes can be applied based on the specific requirements of the application.
- Drilling and Routing: Holes are drilled for vias and component mounting. The board is then routed to its final shape and size.
- Final Inspection and Testing: Every IMS PCB undergoes rigorous electrical testing and visual inspection to ensure it meets our high-quality standards.
Advanced Techniques Used by JHYPCB:
As an innovative IMS PCB manufacturer, we employ several advanced techniques to enhance the quality and performance of our IMS PCBs:
- Vacuum Lamination: This technique ensures uniform bonding between layers, crucial for optimal thermal performance.
- Laser Drilling: For ultra-precise hole drilling, especially important in high-density designs.
- X-ray Inspection: To verify the internal structure and integrity of multi-layer IMS PCBs.
The PCB Manufacturing Process Guide offers valuable insights for a more technical deep-dive into PCB manufacturing processes.
Ensuring High-Quality and Reliability:
Quality and reliability are paramount in IMS PCB manufacturing. At JHYPCB, we implement several measures to ensure the highest standards:
- Strict Quality Control: We adhere to IPC standards and have implemented a rigorous quality management system.
- Advanced Testing Equipment: Our facility is equipped with state-of-the-art testing apparatus to verify both electrical and thermal performance.
- Continuous Process Improvement: We constantly refine our manufacturing processes based on the latest industry developments and customer feedback.
- Skilled Workforce: Our team of experienced engineers and technicians undergoes regular training to stay at the forefront of IMS PCB manufacturing technology.
As your trusted IMS PCB manufacturer, JHYPCB is committed to delivering products that not only meet but exceed your expectations. Our meticulous manufacturing process ensures that each IMS PCB we produce is a testament to our dedication to quality and innovation.
Ready to experience the JHYPCB difference in IMS PCB manufacturing? Contact us today to discuss your project requirements. Let our expertise as a leading IMS PCB manufacturer guide you towards the optimal thermal management solution for your electronics.
Thermal Management Benefits of IMS PCBs
As a leading IMS PCB manufacturer, JHYPCB is at the forefront of thermal management solutions in the electronics industry. The superior heat dissipation capabilities of IMS PCBs are revolutionizing how we approach thermal challenges in electronic devices. Let’s delve into the significant thermal management benefits that make IMS PCBs a game-changer.
How IMS PCBs Improve Heat Dissipation:
IMS PCBs, as designed and produced by an expert IMS PCB manufacturer like JHYPCB, offer exceptional heat dissipation properties:
- Efficient Heat Spreading: The metal base layer, typically aluminum or copper, acts as an efficient heat spreader. It quickly conducts heat away from components, distributing it across the entire board.
- Direct Thermal Path: The thin dielectric layer provides a direct thermal path from the components to the metal base. This minimizes thermal resistance, allowing heat to transfer more efficiently.
- Large Surface Area: The metal base of an IMS PCB effectively increases the surface area available for heat dissipation, enhancing overall cooling efficiency.
- Reduced Thermal Resistance: Compared to traditional FR-4 boards, IMS PCBs have significantly lower thermal resistance. This allows for more efficient heat transfer from the components to the ambient environment.
Comparison with Traditional Cooling Methods:
As an experienced IMS PCB manufacturer, we often compare IMS technology with traditional cooling methods:
- Heat Sinks: While effective, heat sinks add bulk and weight to designs. IMS PCBs can often eliminate the need for separate heat sinks, resulting in more compact and lightweight designs.
- Cooling Fans: Fans are noisy, consume power, and can be points of failure. IMS PCBs provide passive cooling, increasing reliability and reducing power consumption.
- Traditional PCBs with Thermal Vias: Thermal vias can improve heat dissipation in standard PCBs, but they’re far less efficient than the direct thermal path provided by IMS PCBs.
Long-term Benefits for Electronic Devices:
Choosing JHYPCB as your IMS PCB manufacturer brings long-term benefits to your electronic devices:
- Increased Reliability: Better thermal management leads to cooler operation of components, significantly increasing their lifespan and the overall reliability of the device.
- Enhanced Performance: Cooler operating temperatures allow components to perform at their peak, potentially enabling higher clock speeds or increased power output.
- Compact Designs: The efficient cooling provided by IMS PCBs often allows for more compact designs, a crucial factor in many modern electronic applications.
- Energy Efficiency: By managing heat more effectively, IMS PCBs can contribute to the overall energy efficiency of a device, potentially reducing power consumption.
- Cost-Effectiveness: While the initial cost of an IMS PCB may be higher, the long-term benefits often result in overall cost savings through increased reliability, reduced need for additional cooling components, and improved energy efficiency.
As your trusted IMS PCB manufacturer, JHYPCB is committed to helping you harness these thermal management benefits in your electronic designs. Our expertise in IMS PCB manufacturing allows us to tailor solutions to your specific thermal challenges, ensuring optimal performance and reliability for your products.
Ready to revolutionize your thermal management strategy? Reach out to our team of experts today. Let JHYPCB, your go-to IMS PCB manufacturer, guide you in implementing these advanced thermal management solutions in your next project. Experience the difference that superior heat dissipation can make in your electronic devices’ performance and longevity.
Designing with IMS PCBs: Best Practices
As an experienced IMS PCB manufacturer, JHYPCB understands that designing with IMS PCBs requires a unique approach. To help you maximize the benefits of this technology, we’ve compiled a set of best practices for designing with IMS PCBs. Let’s explore these key considerations to ensure your design leverages the full potential of IMS technology.
Key Considerations for IMS PCB Design:
- Component Placement: When designing an IMS PCB, strategic component placement is crucial. As a knowledgeable IMS PCB manufacturer, we recommend:
- Placing high-heat components in areas with the best thermal dissipation
- Avoiding clustering heat-generating components
- Considering the metal base’s heat spreading properties in your layout
- Thermal Management: Effective thermal management is at the core of IMS PCB design. Consider:
- Using thermal simulations to optimize heat dissipation
- Incorporating thermal relief patterns for better heat distribution
- Designing with appropriate copper weight for optimal heat spreading
- Electrical Isolation: While focusing on thermal properties, don’t overlook electrical isolation. As an IMS PCB manufacturer, we stress the importance of:
- Maintaining proper clearance between high-voltage components
- Using appropriate dielectric thickness for your voltage requirements
- Considering creepage and clearance distances in your design
- Manufacturing Constraints: Understanding manufacturing constraints is crucial. At JHYPCB, our experience as an IMS PCB manufacturer allows us to guide you on:
- Minimum trace width and spacing capabilities
- Drill size limitations and aspect ratio considerations
- Surface finish options and their impact on assembly
Working with JHYPCB’s Design Team:
As your partner IMS PCB manufacturer, JHYPCB offers comprehensive design support:
- Design Review: Our expert team can review your designs, offering suggestions for optimization from both a thermal and manufacturing perspective.
- Thermal Simulation: We provide advanced thermal simulation services to validate your design’s thermal performance before production.
- Material Selection Guidance: Our team can help you choose the optimal base metal, dielectric material, and copper weight for your specific application.
- DFM (Design for Manufacturability) Support: We offer guidance on designing your IMS PCB for optimal manufacturability, helping you avoid common pitfalls. Learn more about our DFM support services.
Common Pitfalls to Avoid:
Based on our extensive experience as an IMS PCB manufacturer, here are some common pitfalls to watch out for:
- Overlooking Thermal Expansion: IMS PCBs can have different thermal expansion rates than components. Consider this in your design to prevent stress on solder joints.
- Ignoring Edge Plating: Edge plating can be crucial for certain applications. Don’t overlook this option if your design requires it.
- Underestimating Dielectric Thickness: While a thinner dielectric improves thermal performance, it may compromise electrical isolation. Strike the right balance for your application.
- Neglecting Copper Weight: Copper weight significantly affects thermal performance. Don’t default to standard weights without considering your thermal requirements.
For more insights on PCB design best practices, you might find this PCB Design Guidelines article from Altium helpful.
At JHYPCB, we’re not just an IMS PCB manufacturer – we’re your design partner. Our team is committed to helping you create IMS PCB designs that meet your thermal management needs while ensuring manufacturability and reliability.
Conclusion
As we wrap up our comprehensive exploration of IMS PCB technology, it’s clear that the role of a specialized IMS PCB manufacturer like JHYPCB is more crucial than ever in today’s rapidly evolving electronics landscape.
Recap of JHYPCB’s Expertise in IMS PCB Manufacturing:
Throughout this article, we’ve highlighted how JHYPCB, as a leading IMS PCB manufacturer, brings unparalleled value to your thermal management solutions:
- Cutting-edge manufacturing capabilities
- Extensive experience across various industries
- Commitment to quality and reliability
- Innovative approach to IMS PCB design and production
- Dedication to staying ahead of future trends
Our expertise as an IMS PCB manufacturer extends beyond just production. We offer comprehensive support from initial design consultation through to final product delivery, ensuring that your thermal management needs are met with precision and efficiency.
The JHYPCB Advantage:
Choosing JHYPCB as your IMS PCB manufacturer means partnering with a company that:
- Understands the critical role of thermal management in modern electronics
- Offers customized solutions tailored to your specific application needs
- Provides ongoing support and collaboration throughout your project lifecycle
- Continuously innovates to bring you the latest in IMS PCB technology
Learn more about the JHYPCB advantage and how we stand out as an IMS PCB manufacturer.
Ready to take your thermal management to the next level? JHYPCB, your trusted IMS PCB manufacturer, is here to help. Whether you’re dealing with high-power LEDs, electric vehicle components, 5G equipment, or any other application requiring superior thermal performance, we have the expertise and capabilities to deliver the perfect solution.
Contact our team of experts today to discuss your IMS PCB needs. Let’s work together to create innovative, efficient, and reliable thermal management solutions that give your products a competitive edge in the market.
Choose JHYPCB – Where innovation meets thermal excellence in IMS PCB manufacturing.
Related Posts
- Types of PCBs: Comprehensive Guide to Printed Circuit Boards
- Get Your PCB Prototypes Rapidly with Our Fast Turn Services
- China’s Leading Manufacturer and Assembler of LED PCBs
- LED PCB Design Guide: Tips and Best Practices for Manufacturers
- The Best Materials for LED PCB Boards
- Applications of Aluminum PCB: A Comprehensive Overview
- Aluminum PCBs: The Optimal Thermal Solution for High-Power Electronics
- The Ultimate Guide to Aluminum PCB Manufacturing Process
- The Importance of Choosing the Right Aluminum PCB Manufacturer
- An Introduction to Aluminum Substrate PCB Types
- A Comparison of Aluminum Core PCBs and Copper Core PCBs
- Comparative Analysis of Aluminum PCB and FR-4 PCB
- What Are The Types of Metal Core PCBs?
- Metal Core PCB vs. FR4: What is the Different?
- Metal Core PCB Manufacturing Process Step by Step
- Design Considerations for Metal Core PCBs: Tips and Tricks for Optimal Performance
- What is Copper Based PCB?