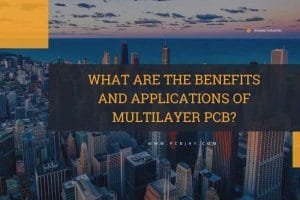
PCB Electronic Manufacturing Services
PCB for High Current Applications
JHYPCB is a professional PCB manufacturing and assembly service provider in China, specialized in high-current PCBs. Our services cover PCB design, manufacturing, testing, and assembly.
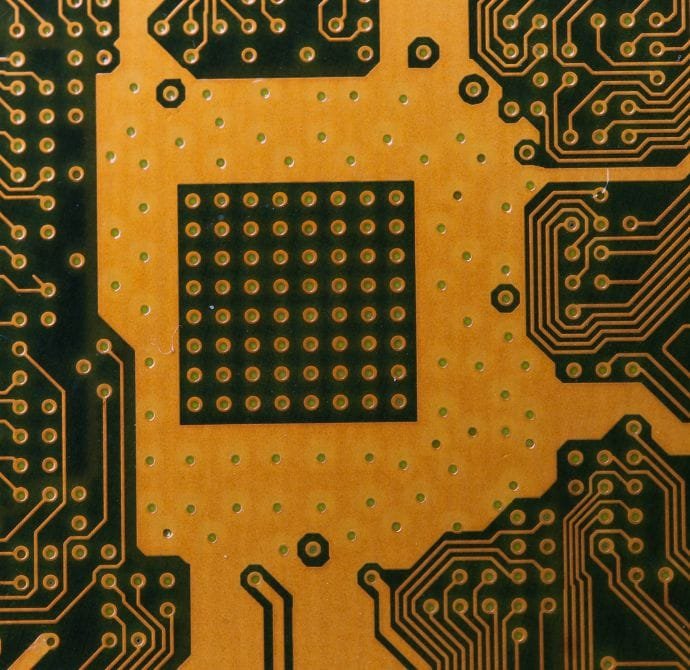
Your Trusted PCB Manufacturer
Professional High-Current PCB Manufactuer
JHYPCB is a professional PCB manufacturing and assembly service provider in China, specializing in the manufacturing, assembly, and testing high-current PCBs. Whether you are just starting or have been deeply involved in this field for years, we offer customized PCB solutions that meet your needs. With advanced production equipment and a professional team, we provide customers with high-quality, efficient, and reliable cooperation experience.
Printed Circuit Board Definition
What is a PCB?
PCB, or Printed Circuit Board, is a board used for connecting and supporting electronic components. It is made of insulating and conductive materials. It is produced through printing and etching to create circuits, holes, and pads, which connect electronic components to form complex circuit functions. PCBs have the advantages of simple structure, reliable connectivity, stable quality, short production cycle, and low cost, and they are widely used in modern electronic equipment. JHYPCB is a professional PCB manufacturing and assembly service provider with rich experience and an excellent technical team. We are committed to providing customers with high-quality PCB products and services and becoming your trusted partner.
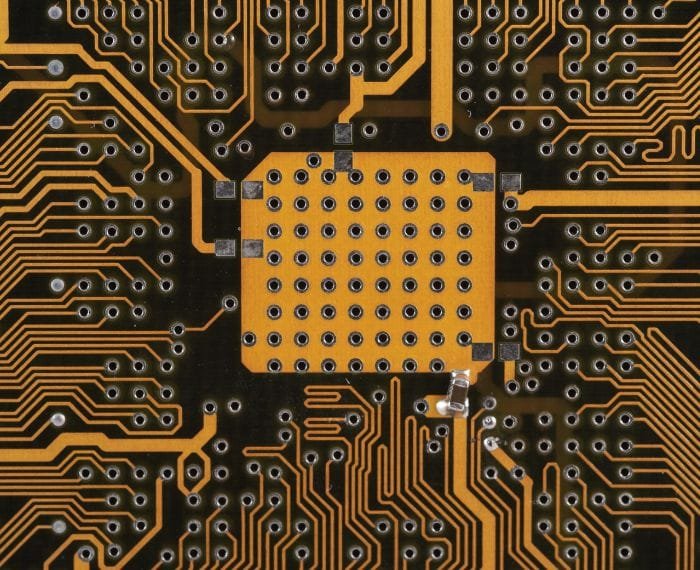
What is High-Current PCB?
High-Current PCBs are printed circuit boards designed to carry higher levels of electric current with improved thermal management. They achieve this by increasing the thickness of copper foil, controlling the temperature of the board, and adding heat sinks to the design.
High-Current PCBs offer the following features and benefits:
Higher current and thermal loads: Compared to traditional PCBs, High-Current PCBs can handle higher electric current and thermal loads, making them ideal for use in high-power applications such as renewable energy, power electronics, automotive, and telecommunications.
Higher efficiency and lower power consumption: With improved thermal management and electrical conductivity, High-Current PCBs consume less energy, making them more efficient and sustainable.
Improved thermal management: High-Current PCBs can efficiently dissipate and transfer the heat generated by high-power electronics, reducing the risk of damage to the board due to excessive heat buildup.
Greater design flexibility: With its enhanced design flexibility and versatility, High-Current PCBs can adapt and accommodate different sizes, shapes, and interconnect schemes depending on specific application needs.
In summary, High-Current PCBs are widely used in high-power applications due to their higher current-carrying capacity, better thermal management, and higher efficiency.
Application Range of High-Current PCBs
The application range of high-current PCBs is becoming increasingly wider in electronics products. Here are some of the application areas of high-current PCBs:
- High-Current PCBs are widely used in a range of industries, including automotive, power electronics, renewable energy, telecom, and computing.
- In the automotive industry, High-Current PCBs are used for electric vehicle powertrain systems, battery management, and motor control.
- In power electronics, High-Current PCBs are used for high-frequency switching circuits, DC-DC converters, and power inverters.
- In renewable energy, High-Current PCBs are used for solar panel inverters and wind turbine power converters.
- In telecom and computing, High-Current PCBs are used for high-speed data transmission, server power distribution, and GPU power management.
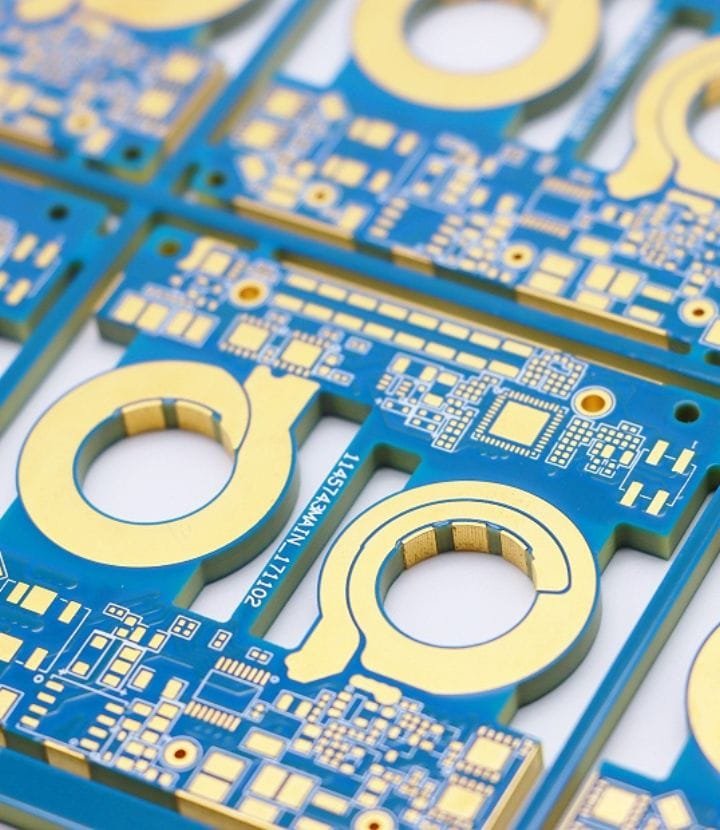
Get a Free Quick Quote
Challenges of High-current PCBs
Engineers face several challenges affecting their performance and reliability when designing high-current printed circuit boards. These challenges stem primarily from the increased currents and heat loads that high-current PCBs are designed to handle. Some common challenges include:
- Thermal management: Managing heat generated by high currents is one of the primary challenges of high-current PCB design. As it accumulates, it can cause damage to components and lead to reliability issues over time.
- Trace width optimization: The width of traces and their placement influence the current-carrying capacity of the board. Finding the optimal trace width and spacing is crucial to minimizing resistance and accommodating high-current levels.
- Component placement: Components that generate high heat, such as power transistors, must be spaced strategically to dissipate heat efficiently and avoid hotspots on the board.
- Material selection: Choosing PCB substrate and copper thickness is crucial for optimal thermal and electrical performance. High-current PCBs require materials that can withstand higher temperatures and provide low-resistance electrical paths.
- Cost: High-current PCB designs can be more expensive as they require higher-quality materials, specialized tooling, and process control in manufacturing.
Challenges and Key Points in Manufacturing High Current PCBs
The manufacturing of high current PCBs is a complex process, which requires a series of special manufacturing methods and processes to ensure the quality and reliability of the PCB. The following are the key points for the manufacturing of high current PCBs:
- Material selection
Material selection is a critical part of high current PCB manufacturing. PCB material’s thermal conductivity, electronic performance, mechanical strength, and environmental durability need to be considered in order to provide high-quality base material and copper-clad laminate that can maintain good performance under high current and temperature conditions. - Layout optimization
In the process of PCB manufacturing, the circuit layout needs to be optimized by arranging reasonable through and signal lines between various components and parts, providing sufficient grounding and power layers on both sides of the PCB to avoid negative effects such as electromagnetic interference and interaction between circuits. - Thick copper foil
In the manufacturing of high current PCBs, it is usually necessary to use thick copper foil to increase the PCB’s conductivity and heat dissipation performance. At the same time, it can also improve the mechanical strength of the PCB surface, preventing the PCB from breaking or getting damaged when in high voltage and vibration environments. - Ensuring thickness uniformity
In the manufacturing process of high current PCBs, it is necessary to ensure the uniformity of the single-sided thickness of significant copper foil layers and the thickness matching among various boards to avoid problems such as uneven voltage difference and current distribution, which can lead to unstable or faulty circuit performance. - Professional manufacturer
In the manufacturing process of high current PCBs, a professional manufacturer needs to be selected to ensure that the production company has sufficient experience and a professional team to guarantee high-quality manufacturing. At the same time, it is necessary to comply with European and international standards such as IPC-2221, IPC-2222, and UL during the production process.
Frequently Asked Questions about high current PCBs
What is a high current PCB?
A high current PCB is a printed circuit board designed to handle large amounts of electrical current.
What is the maximum current a high current PCB can handle?
大电流PCB可以处理的最大电流没有固定值.这取决于各种因素,例如铜迹线的厚度、电路板尺寸、使用的材料、散热效率。
What are the challenges in designing high current PCBs?
Designing high current PCBs can be challenging, and some of the common issues include managing heat dissipation, optimizing trace widths, arranging component placement, selecting suitable materials, and ensuring good electrical and mechanical performance.
What materials are commonly used for high current PCBs?
Materials such as copper, aluminum, and other conductive metals are commonly used for high current PCBs due to their high electrical conductivity. Additionally, some insulating materials such as FR-4 and ceramic substrates are also used for their excellent thermal and mechanical properties.
Can high current PCBs be manufactured using standard PCB fabrication processes?
High current PCBs often require additional or modified fabrication steps such as thicker copper plating and special lamination techniques. Therefore, manufacturing high current PCBs requires specialized expertise and equipment.
How can I ensure the reliability of high current PCBs?
To ensure the reliability of high current PCBs, it is essential to test the boards during the design and prototyping phases to identify any potential issues. Additionally, selecting high-quality materials, optimizing design for thermal management, and adhering to industry standards can significantly improve the reliability of high current PCBs.
