PCB Technology
What are Blind & Buried Vias in Multilayer PCB?
In the realm of PCB technology, you may have come across the terms blind vias and buried vias. The question arises, what exactly do these terms refer to, and how do they impact your project? This article aims to provide you with the answers.
Printed Circuit Boards are an indispensable component in the modern electronics industry, as they provide a physical platform for electronic components to interact. PCBs are essential in the manufacturing process of all electronic devices that have printed circuitry, from cell phones to computers, automotive components to aerospace systems. BLIND AND BURIED VIAS are specialized types of vias used in PCBs that play an important role in their functionality. These vias enable the interconnection of conductive layers in areas where traditional through-hole vias are not appropriate. In this discussion, we will delve into the specifics of blind and buried vias, their manufacturing methods, and their advantages over other types of vias.
Table of Contents
Add a header to begin generating the table of contents
Understanding Blind & Buried Vias
Blind & Buried Vias are types of specialized via holes used in PCBs to improve connectivity and reduce board area for compact devices. These vias connect the outer layer of a PCB to inner layers, without passing through the entire board.
Blind vias are partially drilled from either the top or the bottom side of the PCB, and are stopped at a specific depth. Buried vias, on the other hand, are drilled entirely within the inner layers of the PCB, and do not penetrate the outer layer.
Both types of vias offer advantages in terms of reducing the size of the board and increasing its density, as they provide a means to connect multiple layers of a PCB. However, it is important to carefully consider their design and placement, as they can affect the overall cost and manufacturability of the PCB.
When designing a board that includes blind and buried vias, it is important to consider factors such as the number of layers, the thickness of the board, and the placement and sizes of these vias. This can have an impact on the complexity of the manufacturing process, as well as on the cost of the final product.
Overall, blind and buried vias provide an efficient way to create smaller and denser PCBs, but must be carefully designed and placed to ensure their effectiveness and manufacturability. It’s important to work with an experienced PCB manufacturer, such as JHYPCB, who can offer guidance and expertise in the design and manufacturing process.
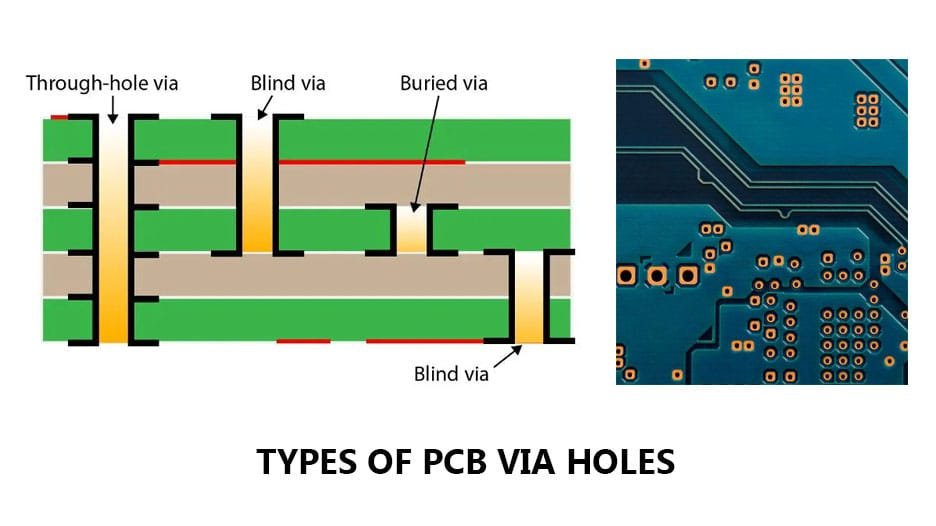
What Are Blind Vias?
A Blind via is a type of via that connects the top or bottom layer of a PCB to one or more inner layers, but does not extend through the entire board. The via is drilled from the surface of the PCB and only extends partway into the board, terminating at a specific depth. This type of via is referred to as “blind” because it is not visible from the opposite side of the board.
Blind vias work by using a modified drill bit that can only penetrate a specific depth into the board. Typically, Blind vias are only drilled a few layers deep, making them a great option for creating connections between outer-layer components and inner-layer traces without passing through the entire board.
When designing Blind vias, there are several important considerations to keep in mind. These include the type of drill bit used, the thickness of the board, and the applicable layer configurations. Blind vias typically require more advanced and expensive drilling techniques than traditional through-hole vias, and may also have smaller diameter requirements due to their compact size.
In addition, there are also limitations to the number and placement of Blind vias due to the constraints of the drilling process. As a general rule, designers typically restrict Blind vias to a single layer or a small group of adjacent layers in order to minimize complexity and ensure manufacturability.
Despite these limitations, Blind vias are a popular choice in high-density PCB designs where space is at a premium. They can be used to connect surface-mount components on the outer layers of the board to inner-layer signals and power traces, which can help reduce the overall size of the board and improve its performance.
Overall, Blind vias are a useful tool for PCB designers looking to create compact and efficient PCB layouts. By carefully considering their design and placement, designers can ensure that Blind vias provide reliable connections while also meeting their manufacturing requirements.
Advantages of Blind Vias
Blind vias are a crucial aspect of modern PCB design. They are drilled from one of the outer layers of the PCB and only penetrate through a portion of the board. Here are some advantages of using blind vias:
Space-saving: Blind vias provide more space on the surface of the board by allowing designers to use multiple layers without requiring vias to go through the entire circuit board. This allows for the design of smaller and more compact PCBs, which are particularly useful for devices that have limited space.
Better signal integrity: With blind vias, signals can move between layers more directly and quickly compared to full vias that go through all PCB layers. Blind vias can reduce signal interference and noise, resulting in better signal integrity and reliability of the circuit.
Lower manufacturing costs: Blind vias help in saving manufacturing time and costs. By allowing PCB manufacturers to drill vias in fewer steps, the production process can be made more efficient. This translates into cost savings for manufacturers and ultimately for customers.
Improved thermal performance: Blind vias can help with thermal management by allowing heat dissipation through the vias. This can be useful for designs that have high-power components or require effective cooling.
- Easy to fabrication: Blind vias are easier to manufacture compared to buried vias. The manufacturing process involves drilling the blind vias simultaneously with the through holes for through-hole technology (THT) components. However, manufacturing blind vias still requires precise measurements to ensure the holes are not drilled too deep or too shallow.
- Best for SMT boards: Blind vias are well-suited for SMT boards because they can connect SMT components on the top and bottom layers of the circuit with internal layers. This reduces the length of the signal trace, minimizes cross-talk, and reduces the amount of noise in the circuit.
- Reliability: As we are aware, Blind Vias only traverse through a precise section of the PCB, making them less likely to impact the general dependability of the printed circuit board. This is due to the fact that Blind Vias do not pass entirely through the PCB, resulting in reduced potential for mechanical issues, such as drill breakouts and other manufacturing defects, which may be encountered in circuit boards with Through Holes and Buried Vias.
Disadvantages of Blind Vias
Increased complexity in the manufacturing process compared to standard vias due to the need for added drilling and plating steps, which can increase production time and cost.
Limited flexibility in design, as blind vias require specific layer alignment and stack-up configurations, which can limit the number of layers and design options available.
Difficulties with repair and rework, as the partial drill depth of blind vias can make it challenging to remove and replace components without damaging the board.
Limited depth and aspect ratio options compared to through-hole vias, which can limit the capacity of the board to handle high-speed signals or heavy currents.
Risk of plating defects, as the partial plating process used in the creation of blind vias can lead to variations in plating depth or incomplete hole filling, which can negatively impact the electrical performance and reliability of the board.
Minimum Drilled Hole Size for Blind Vias
Layer Thickness | Class 1 | Class 2 | Class 3 |
---|---|---|---|
<0.1mm | 0.10mm | 0.10mm | 0.20mm |
0.10-0.25mm | 0.15mm | 0.20mm | 0.30mm |
0.25mm | 0.20mm | 0.30mm | 0.40mm |
What Are Buried Vias?
A Buried via is a type of via that is located between the layers of a multilayer PCB, and does not extend to the surface. Unlike blind vias, which connect an outer layer to an inner layer, buried vias only connect inner layers of the PCB.
Buried vias work by drilling a hole through the inner layers of the PCB, and then filling the hole with conductive material, such as copper, to create an electrical connection between two or more layers. The via remains hidden between the layers and cannot be seen on the surface of the board.
Design considerations for buried vias include the number of lamination cycles required. Since buried vias are located between inner layers, additional lamination cycles may be needed to create the multilayer structure. This can add to the cost and complexity of the PCB manufacturing process.
Buried vias are typically used in applications where blind vias are not applicable, such as when the PCB is too thick, or in cases where extra layer pair costs need to be avoided. They are also used in high-density applications, where space is at a premium and the routing of traces would be difficult without the use of vias.
Advantages of Buried Vias
- Saves Space: One advantage of using buried vias instead of blind vias and through-hole vias is that they save space. This extra space can be utilized for routing other signal traces.
Reduced layer count: Buried vias can reduce the overall layer count in a design as they allow for vertical connections between inner layers. This can lead to smaller and lighter boards, as well as lower manufacturing costs.
Improved signal performance: Buried vias can be used to reduce signal reflections and crosstalk. This is because signals can be routed more directly between inner layers without needing to travel through additional layers, which can introduce noise and interference.
Increased reliability: Buried vias can improve the reliability of a PCB. This is because they avoid the risk of punched holes or drilled vias that can lead to damage to surrounding components or cause electrical shorts.
Enhanced thermal management: Buried vias can be used to improve the thermal management of a PCB. This is because they can allow heat to be dissipated through the layers more efficiently, which can help to prevent hot spots and ensure that components operate within their specified temperature range.
Reduced electromagnetic interference (EMI): Buried vias can reduce the amount of EMI produced by a PCB. This is because they can provide a more direct path for signals, which reduces the need for long traces that can act as antennas and radiate EMI.
Disadvantages of Buried Vias
Increased manufacturing complexity: The process of creating buried vias is more complicated than that of regular vias. This can lead to longer manufacturing time and increased cost.
Limited accessibility for testing and probing: Since buried vias are not visible on the surface of the board, they can be more difficult to test and probe compared to other types of vias.
Limited rework options: Repairing or modifying a buried via can be difficult and may require costly rework processes.
Increased risk of reliability issues: Because buried vias are hidden within the layers of the board, any reliability issues that arise with these vias can be harder to detect and correct.
Not suitable for all types of designs: Buried vias may not be necessary or appropriate for all types of designs, particularly those with low-density routing or those with a limited number of layers.
- Expensive: Buried vias are costly to manufacture because of their intricate and time-consuming process.
Minimum Drilled Hole Size for Buried Vias
Layer Thickness | Class 1 | Class 2 | Class 3 |
---|---|---|---|
<0.25mm | 0.10mm | 0.10mm | 0.15mm |
0.25-0.5mm | 0.15mm | 0.15mm | 0.20mm |
0.5mm | 0.15mm | 0.20mm | 0.25mm |
What is Stacked Via and Microvia?
Stacked vias are a type of via structure in PCB design that include one or more vias vertically stacked on top of each other. Stacked vias can be used in conjunction with both blind and buried vias to provide additional routing options and to reduce the complexity of the board layout.
One benefit of using stacked vias is that they can help reduce the number of layers required in a PCB design. By stacking multiple vias on top of each other, the same signal can be routed between multiple layers without using additional layers in the board design. This can help to reduce the overall cost and complexity of the board, especially for high-density designs.
Another benefit of using stacked vias is that they can help to improve signal integrity by reducing the length of the signal path and minimizing the parasitic capacitance and inductance in the routing. This can help to improve the performance of the board, especially at high frequencies.
However, there are also some limitations to using stacked vias, including the increased complexity of the board layout and routing, the potential for signal crosstalk between the stacked vias, and the increased cost and time required for manufacturing and testing the board. Additionally, stacked vias may not be suitable for all types of designs, and the choice of via structure should be carefully considered based on the specific requirements of the design.
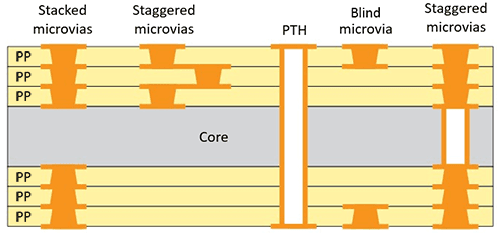
Benefits of Stacked Microvia
In high-speed digital circuits and communication systems, ensuring optimal signal integrity is critical. Stacked micro vias offer significant advantages over traditional vias by providing a shorter, direct path for signals to travel between layers of a PCB. As a result, they can reduce parasitic capacitance and inductance, thereby minimizing signal reflection and attenuation. This improvement in overall performance makes stacked micro vias ideal for high-speed applications.
As the size of electronic devices continues to shrink and their performance capabilities increase, effective thermal management becomes increasingly important. Stacked micro vias are also beneficial in this regard. By enabling the creation of a network of micro or thermal vias, heat can be transferred more efficiently from the heat source to other layers of the PCB. This helps dissipate the heat more effectively and prevents localized hotspots from developing, thereby improving the device’s overall thermal management.
Benefits of incorporating micro vias in PCB design
Using micro vias in PCB design offers a multitude of benefits, including:
- Increased circuit density: Micro vias enable more connections to be made in a smaller area on a PCB, allowing for a higher number of components to be placed within the same board size.
- Improved signal integrity: The shortened interconnects created by micro vias can reduce signal loss and noise, resulting in improved signal integrity throughout the circuit board.
- Cost savings: By utilizing micro vias, it may be possible to reduce the number of layers required in a PCB, ultimately lowering production costs. With fewer layers, it’s also possible to reduce the amount of drilling necessary, further decreasing costs.
Potential drawbacks of incorporating micro vias in PCB design
While incorporating micro vias can provide many advantages in PCB design, there are a few potential drawbacks to consider as well, including:
- Increased complexity: The addition of micro vias can introduce a level of complexity in both the manufacturing and testing phases of PCB development. It may be more challenging to build and troubleshoot a circuit board with micro vias, increasing the risk for errors or defects.
- Reduced dependability: Due to their smaller size, micro vias may be more prone to failures than larger vias. Issues such as poor plating quality, inadequate hole fill, and voids in the via can arise during the fabrication process, which can impact the reliability of the stacked micro vias. These issues can lead to electrical opens or shorts, signal integrity problems, and decreased overall dependability of the PCB.
Considerations when constructingPCBs with micro vias
When designing printed circuit boards with micro vias, there are several critical considerations to keep in mind. Firstly, drilling micro vias requires the use of a laser, which necessitates careful management of the laser’s settings to ensure that the holes produced are of the correct size and shape.
Secondly, special plating procedures are required to ensure that micro vias are properly connected to the other layers of the PCB. This is critical for achieving the desired electrical performance of the board.
Thirdly, inspecting micro vias can be challenging, since they are often very small. Therefore, non-destructive testing techniques may be required to verify that they are manufactured and connected correctly.
Finally, material selection is a critical factor in the reliability of micro vias on PCBs. High-quality materials must be used in their construction to ensure their long-term reliability.
IPC-6012 Surface and Hole Copper Plating Requirements
If the PCB has more than two layers, the copper plating on the surface and inside the holes must adhere to the specifications in the following Table for plated through holes, blind vias, and buried vias. This requirement does not apply to microvias. The thickness of the copper plating must be uniform and extend from the walls of the holes onto the outer surface. The guidelines in IPC-A-600 should be consulted to determine the appropriate thickness of the copper plating for the walls of the holes.
IPC-6012 | Class 1 | Class 2 | Class 3 |
---|---|---|---|
Copper -average | 20μm [787μin] | 20μm [787μin] | 25μm [984μin] |
Minimum thin areas | 18μm [709μin] | 18μm [709μin] | 20μm [787μin] |
Minimum Wrap | AABUS | 5μm [197μin] | 12μm [472μin] |
Similarities and differences between blind vias, buried vias, and micro vias.
Similarities:
- Blind, buried, and micro vias are all designed to enhance the space-saving capabilities of traditional through-hole vias on a PCB. This feature allows for a more efficient use of board real estate, resulting in increased component density and more complex PCB designs.
- They provide high-density interconnects, which enable more routing options in high-density designs.
- All three types of vias are smaller in size compared to traditional through-hole vias, typically ranging from a few microns to a few tenths of a millimeter in diameter.
- Specialized fabrication techniques, such as laser drilling and plating, are required for creating the desired via structures. This demands additional manufacturing steps and advanced expertise, which can increase the cost and complexity of the PCB manufacturing process.
- Depending on their placement and routing, all three types of vias have the potential to impact signal integrity. Therefore, careful consideration of via placement and routing is necessary to minimize signal integrity issues.
Differences:
A buried via connects two or more inner layers without extending to the outermost layer, while a blind via connects the outermost layer to one or more of the inner layers. Micro vias, on the other hand, are drilled from the middle of the board and are a more compact option than both blind and buried vias. They connect the neighboring layers of the board. Unlike blind and buried vias that are drilled from either the top or bottom of the board, micro vias are drilled from the middle of the board. However, it’s important to note that producing buried vias is more challenging, time-consuming, and expensive than producing blind or micro vias.
Optimize your PCB layout by selecting the most suitable via type.
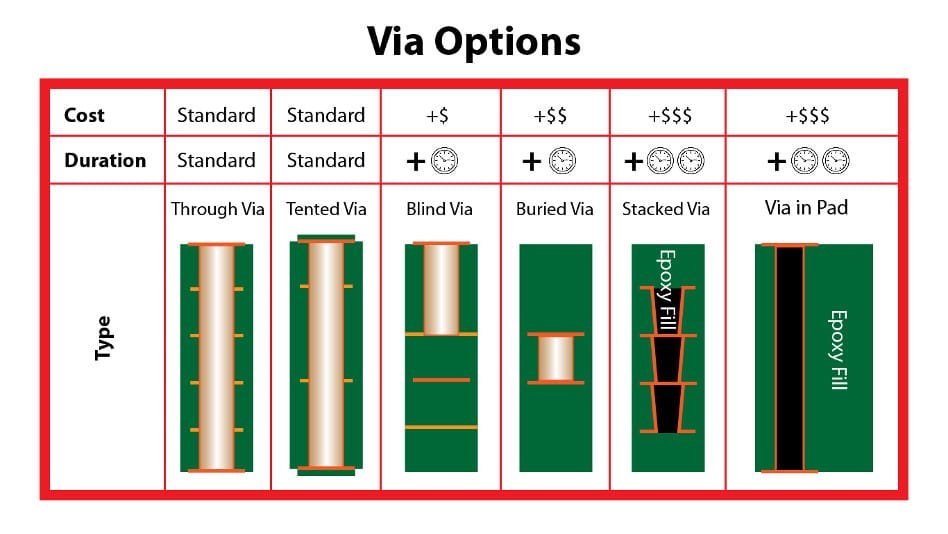
Tented vias are a type of PCB via in which the via holes are fully coated with a protective layer of solder mask material during the manufacturing process. This solder mask layer is applied to the PCB’s copper traces to prevent manufacturing and assembly problems, such as solder bridging or short circuits. When designing a PCB, it’s essential to carefully weigh various factors before deciding on the material to use, as this choice will ultimately affect the PCB’s manufacturing process. These considerations must be taken into account during the design phase to ensure the final PCB meets desired specifications.
- The required density
- The number of board layers
- Signal speed,
- and the available budget is all factors to be considered while making this selection.
Blind and buried vias are better suited for high-density systems that have many layers. The use of blind and buried vias has become more prevalent. In contrast, micro vias are more appropriate for designs with fewer layers and smaller components. When it comes to high-speed communications, it is crucial to regulate impedance, which often requires the use of multiple types of vias.
Blind, buried, and micro vias are vital components for PCB designers looking to create high-density, compact, and high-performance boards. Despite the additional manufacturing costs that may come with their use, these specialized vias are essential for meeting the demands of modern electronics. By comprehending the distinctions and applications of each type of via, designers can optimize their PCB designs and attain top-notch performance in their electronic products.
PCB Via Hole Manufacturing Capabilities
We utilize a mix of depth-controlled laser drilling and mechanical NC drilling to produce blind and/or buried vias. The manufacturing capabilities for both standard PCBs and HDI PCBs are shown in the following table.
Blind or Buried Via | Aspect Ratio | Ø min | Ø max | Via Pad | Annular Ring |
---|---|---|---|---|---|
Blind Via (mechanical) | 1:1 | 200μm | 300μm | 400μm | 100μm |
Special Blind Fabrication | 1:1.2 | 150μm | 150μm | 350μm | 100μm |
Blind Via (Laser) | 1:1 | 100μm | 100μm | 280μm | 90μm |
Buried Via (mechanical) | 1:10 | 200μm | 400μm | 400μm | 100μm |
Special Buried Fabrication | 1:12 | 150μm | 400μm | 330μm | 90μm |
Please click the link to view our advanced PCB fabrication process and capabilities.
FAQs on Blind & Buried Vias
What is PCB Vias?
PCB vias are small holes in a printed circuit board that allow electrical connections between different layers of the board. They are typically filled with conductive material and serve as pathways for electrical signals to move between different layers of the board. Vias are an important aspect of modern PCB design, as they allow for dense layouts and increased functionality in a compact form factor.
What are Microvias?
Microvias are a type of via used in modern PCB designs that are much smaller in size compared to traditional vias. Microvias typically have diameters ranging from 50 microns to 150 microns, and they are used to connect surface mount components to inner layers of a PCB. Microvias are preferred in high-density designs because they take up less space and allow for more routing channels compared to traditional vias. They also have improved electrical performance, as their smaller size reduces the amount of parasitic capacitance and inductance in the PCB.
Why Do We Need Blind and Buried Vias?
Blind and buried vias are used in PCB designs to save space and improve signal integrity. They allow designers to connect components on different layers of the PCB without having to route traces all the way through the board or use larger, more expensive through-hole vias. Blind vias only go partway through the PCB, while buried vias are completely contained within the PCB layers and do not go all the way through. This allows for more closely spaced components and shorter signal paths, which can improve performance and reduce crosstalk and noise. Additionally, blind and buried vias can reduce the overall size and weight of the PCB, which is especially important for modern electronic devices where compact design is crucial.
How are blind vias made?
Blind vias are made using special drilling techniques that drill only to a certain depth of the PCB. This is usually done using a laser drill or a mechanical NC drill with depth control.
What are the advantages of using blind vias?
Blind vias consume less space on the board and cost less to manufacture than through-hole vias. They also allow for higher routing densities, shorter signal paths and faster signal speeds.
What are the limitations of using blind vias?
Blind vias can add an extra step to the assembly process and may add a higher cost due to the specialized drilling equipment required. Additionally, the aspect ratio of the via may limit the depth and size of the blind via.
How do you calculate the size and depth of a blind via?
There are many factors to consider when calculating the dimensions of a blind via, including the thickness of the PCB, the aspect ratio of the via, and the size of the pin or via barrel. Design rules for a specific PCB manufacturer should be used to ensure the correct size and depth of the blind via.
What are buried vias?
Buried vias are copper-plated holes drilled in the PCB that do not extend through the entire thickness of the board. They are covered by additional layers of copper and insulation during the board production process.
What is a blind via?
A blind via is a hole that only goes partway through the PCB, connecting one or more layers of the PCB but not going all the way through.
What are the advantages of buried vias?
Buried vias can help reduce the size of the PCB, as they allow for more wiring and electrical connections in a smaller space. This can lead to more compact and efficient electronic devices. Additionally, because they do not extend through the entire board, they can help improve the structural integrity of the PCB.
What is the difference between buried vias and through-hole vias?
Through-hole vias extend through the entire thickness of the board, while buried vias do not. This means that buried vias can provide more efficient use of space and improved structural integrity, but they also require more complex manufacturing processes.
How are buried vias made?
Buried vias are made by drilling small holes in the PCB, filling them with copper, and then covering them with additional layers of insulation and copper. This requires a more complex manufacturing process than through-hole vias.
What is the cost of using buried vias?
Because buried vias require more complex manufacturing processes, they can be more expensive than through-hole vias. However, the cost difference might be offset by the advantages of using them (such as improved space utilization and structural integrity).
How are buried vias tested?
Testing buried vias can be difficult because they are not visible from the surface of the board. One way to test them is to use x-ray equipment to inspect the inner layers of the board. Another way is to use micro-sectioning, which involves cutting and polishing a sample of the board to inspect the internal layers.